挥发性有机化合物VOC是大气污染物的重要组成部分。目前,国内外VOCs常用的治理方法主要有 活性炭变压吸附法、光催化氧化、溶液吸收法、高温氧化法等。其中,高温氧化法处理 VOC 废气的效率*高,也被普遍采用。蓄热式氧化炉(RTO),是目前国内外比较流行的VOC废气高温氧化治理设备。主流的RTO产品是三厢式塔式RTO。三厢式塔式RTO炉可以兼顾到处理效率和经济性要求。主流的三室式RTO适宜净化VOCs的废气量为10000~30000m3/h。
蓄热式氧化炉的工作原理是:先将废气经过蓄热体预热到一定的温度,然后在在燃烧室将废气的有机物分子氧化燃烧成二氧化碳和水。氧化燃烧产生的高温气体再流经蓄热体,使蓄热体升温,此“蓄热的热量”用于预热新进入炉膛的废气。蓄热体的进出气不断的被换向阀切换,形成周而复始的连续工作。
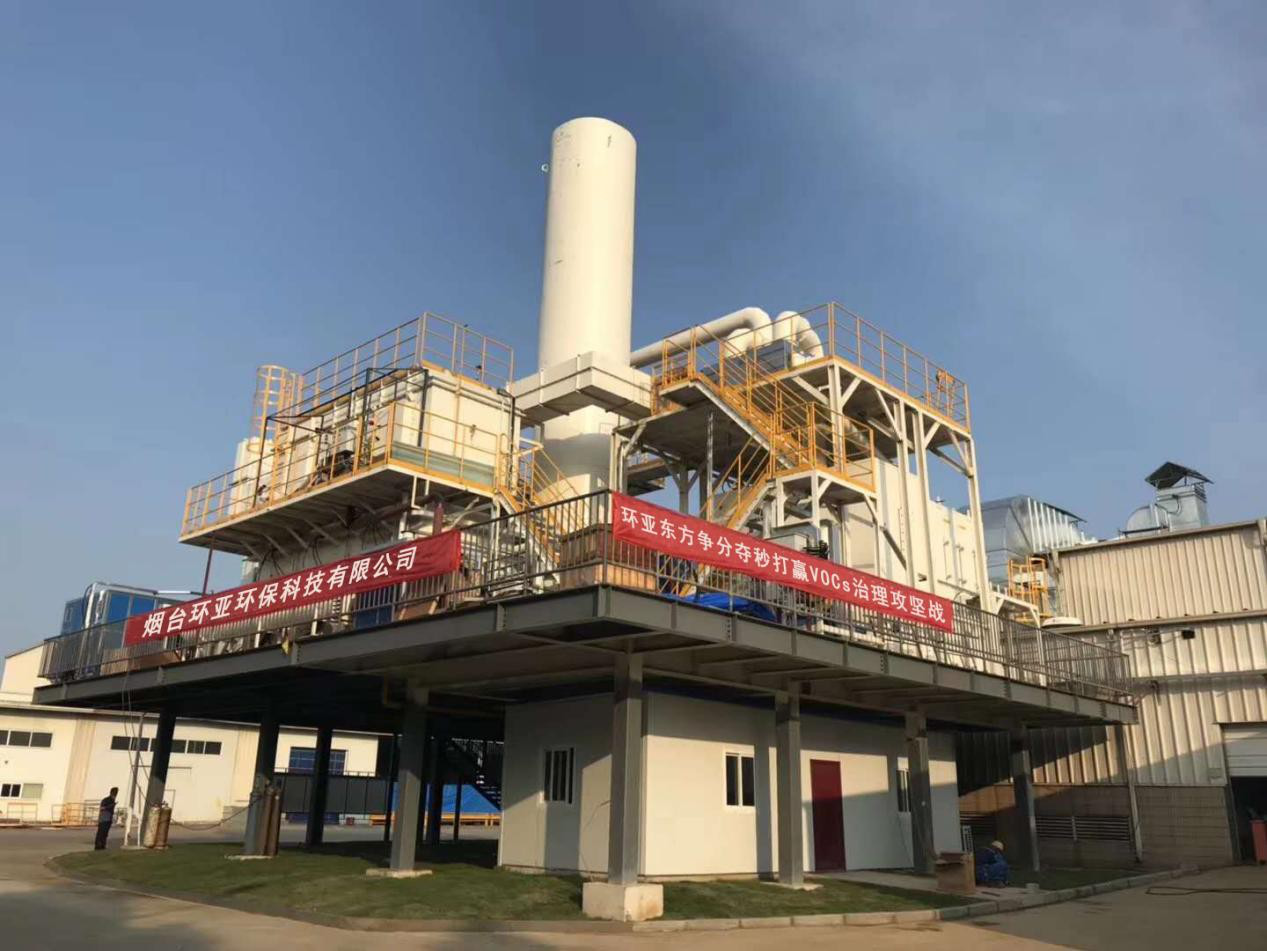
1 RTO低氮环保技术
分析目前国内外学者对低氮技术的研究,能用于RTO上控制NOx排放的技术可分为两类:一类是在燃烧过程中控制有害NOx的生成。第二类,是燃烧后控制有害NOx排放技术。
第*类方法,在燃烧过程中控制有害NOx的生成技术。目前国内外大量推广在燃烧过程的控制氮排放的技术主要可以分为低NOx燃烧器技术与过量空气燃烧技术两种。从NOx的生成机理上来说大部分的NOx是在燃烧过程生成的。技术人员通过改变燃烧器的结构来改变燃烧的条件(通常是改变燃烧区的温度条件)与燃烧过程中的燃料的供应,达到控制NOx生成的目的。研究者根据燃烧工况对NOx排放的影响与NOx的生成机理,从“燃气分级,空气分级,形成明显的燃烧区域,形成烟气回流”等几个方面对燃烧器进行了改进,降低了NOx的排放。重油型燃烧器常采用分段燃烧技术,而气体型燃烧器常采用预混贫燃技术。两者相比后者预混贫燃技术生成的NOx更少。在低氮燃烧器的使用过程中,不同的燃烧脱氮技术的特点不同相应的燃烧器的布置位置也不同。
另一类方法燃烧尾气脱氮脱硝技术这类技术可分为湿法脱氮与干法脱氮两种。
干法脱氮技术是将废气中的NOx还原成N2或者转化为硝酸盐再进行回收利用的方法。目前,国内外干法脱氮的技术主要有选择性催化还原法 SCR技术与非催化还原法SNCR技术。SCR技术的原理是使用了催化剂降低了氧化还原反应的温度,其还原后的N2无污染,处理效果也较好。SCR技术*常用的催化剂是V2O5,MnO2。SCR技术催化剂的选择,需要分析气体中的杂质使催化剂中毒的原因并合理考虑。目前,更为高效耐用的催化剂正在被世界各国所研究探索。SNCR技术的原理是在无催化剂的情况下将还原剂直接喷人炉膛,使废气中氮化物分解成 N2与H2O。SNCR技术的优点是投资较小。但其缺点是耗氨量大,效率不高。
湿法脱氮技术,是先将氮化物转化为N02,再用碱性溶液吸收N02的方法。一般用于吸收N02的设备是填料吸收塔。湿法脱氮的工艺与设备都较为简单,运行费用也较低,无二次污染。根据对NOx的处理方式不同,可将湿法分为氧化吸收法和络合吸收法两大类此法。
将以上两类技术综合应用于RTO系统的设计中能有效降低氮排放,达到节能减排的目的。
2 RTO燃烧与节能技术的优化
目前RTO基本已实现的全自动化运行,因此RTO的节能主要体现在燃烧技术与燃烧尾气热能的回收利用技术。下面从五个方面给出一些优化燃烧与节能的措施。
2.1采用新型高效节能燃烧器,提高燃烧效率
根据燃烧器的结构与性能,将先进的旋流二次雾化技术,独特的分级送风技术与先进的自动控制技术有机的结合起来,改进了燃烧器的燃烧性能,实现了完全燃烧。
2.2催化燃烧技术在RTO上的引用
设计新型炉型将蓄热式氧化技术与催化燃烧技术相结合,使其既具有RTO炉蓄热节能的优点又具有CO炉低温催化燃烧的优点,能使RTO达到节能减排效果。具体的措施:在蓄热厢的顶层设计催化剂放置平台并根据废气种类配置合适的催化剂,让经过蓄热体预热的废气通过催化剂层,形成有机废气的预处理过程,这样有机废气先催化燃烧,后在燃烧室燃烧,形成废气的两次燃烧。催化燃烧不仅能够在一定程度上净化废气,而且燃烧热可以升高废气的温度(一般情况下能够提供有机废气温度15~30℃),在一定程度上有利于节省燃料。
2.3合理设计炉子供气量
从燃烧学的角度讲,要想提高RTO燃烧的效率,就要在燃烧时给RTO炉燃烧室提供合理的供气量。供气量的不足不仅不会充分燃烧,而且会生产大量的一氧化碳;当氧气量过量时,则会使更多的热能随着热空气流失掉,提供了热损失。根据燃烧炉的使用经验来看,废气中的可燃有机物浓度控制在爆炸下限(LEL)25% 的情况下,匹配合理的空气量,不但能够节省燃料,又能使可燃物充分的燃烧,净化尾气减小污染物的排放。
2.4选择合适的燃烧温度
合理选择炉温是RTO优化的一个重要方面。研究表明温度是RTO的转化率的决定因素之一。适当的提高炉温能够使得氧燃烧反应更加完全,更节能。但是,过高的炉温会增加更多的热损失,缩短炉子的使用寿命周期,从而提高了炉子的成本。此外,较高的炉温还会多消耗燃料,同时使得废气净化效果下降,影响废气的达标排放。研究表明,在大于 760℃的温度下,大部分的有机气体分子能被完全破坏,反应更加的充分,氧化生成水和二氧化碳。设计者应该根据不同的废气种类,选择合适的炉温。
2.5炉膛空间的设计优化
除了燃烧温度与废气的浓度影响之外,废气在RTO燃烧室的停留时间也是影响RTO转换效率的一个因素。这是因为有机物的完全氧化燃烧过程需要一定的时间,合理的设计炉膛空间可以使得有机废气在炉膛里有较为合理的停留时间。合理的停留时间,取决于炉膛的截面积,长度,气体的流动速度等因素。根据经验值废气在炉膛内停留1.0~1.3s 可满足废气的排放标准。
3 RTO蓄热体的优化设计
蓄热体是RTO进行能量回收的热载体,蓄热体的性能好坏是RTO能耗的决定性因素。蓄热体的截面积和堆积高度是蓄热厢设计*重要的两个结构参数。蓄热体的结构和性能参数还包括蓄热体的形状、当量直径、比表面积、阻力系数、结构强度、堆积稳定性、耐热冲击性、透热深度、蓄热能力和传热性能和流动阻力特性等。目前,MLM-180,40x40孔蜂窝陶瓷蓄热体与Lantecomb-H 蓄热体被广泛应用,因为与其他类型的蓄热体相比,它们具有较有较高的传热效率。
蓄热体主要存在以下的常见问题:蓄热体的使用寿命较短,蜂窝孔的堵塞,蜂窝蓄热体粘渣,孔壁熔蚀,通孔破裂,蓄热体崩塌与错位等问题。蓄热体损坏的影响因素主要有:蓄热体的材料的物理性能蜂窝蓄热体的使用条件,蓄热体的结构设计与制备工艺。
以为下面就针对RTO蓄热体使用过程中的一些问题,列出了一些优化设计的措施:
(1)蓄热体的选材问题。选择蓄热陶瓷的材料时除了考虑材料的导热性、对流传热性能、膨胀性能以外,还应该考虑不同材质的耐热温度的不同。根据废气燃烧温度和蓄热体的耐热温度合理的选择蓄热体,避免选择软化温度比燃烧问题低陶瓷材料,并且预留一定的温度设计余量。防止选材不当,使蓄热厢的高温端出现高温热融变形与塌陷毁坏的问题。
(2)合理设计蓄热体的布置方案。设计陶瓷蓄热体的布置方案应尽可能的排列整齐,避免出现陶瓷蓄热体的错位排列,造成燃烧中的蓄热体局部高温受热不均匀与高温受热下沉受阻,从而造成局部受力过大而引起蜂窝体的损毁,坍塌堵塞通道。
(3)蓄热体的固定支撑设计。在蓄热体的安装底盘上使用耐高温金属定位支架来固定蓄热体,可以防止在高温条件下长时间的气体热冲击对蓄热体的微观结构产生影响导致蓄热体的热震损毁,阻塞气体流动的通道或者在蓄热室形成空洞,降低蓄热室的传热效果与节能的效率。
(4)合理的布置燃烧器的位置。设计师应该尽可能的采用缩短燃烧火焰的长度的燃烧器。合理布置燃烧器的位置,防止燃烧器火焰的高温区气体火焰直接喷入蓄热体上产生较多的热辐射,烧毁蓄热体。蓄热厢的上层蓄热陶瓷*容易被烧毁,烧毁时应及时更换,防止坍塌。
(5)选择结构合理、质量可靠的燃烧器。防止选择的燃烧器结构不合理或质量不佳,在RTO运行时出现不完全燃烧的废气进入蓄热体进行二次燃烧,进而缩短蓄热体的使用时间。
(6)保障炉体平稳运行,控制炉温稳定在一定范围内。在进气管道上安装浓度在线检测系统严格控制废气的进气浓度,防止高浓度的废气进入燃烧室引起炉温急剧升高,烧毁蓄热体。
版权声明:本网注明来源为“环亚环保”的文字、图片内容,版权均属本站所有,如若转载,请注明本文出处:http://www.ythyhb.com 。同时本网转载内容仅为传播资讯,不代表本网观点。如涉及作品内容、版权和其它问题,请与本网站联系,我们将在及时删除内容。